In today's fast-paced e-commerce world, efficient warehouse management isn't just a luxury—it's a necessity. According to an Emerald Insight study, the number of UK retailers that have not invested in warehouse automation in any way decreased from 32% to 8% in 2023.
A Warehouse Management System (WMS) serves as the backbone of modern logistics operations, transforming how businesses handle inventory, fulfill orders, and deliver customer satisfaction. Let's dive into everything you need to know about WMS and how it can revolutionize your warehouse operations.
Store More, Stress Less: Understanding WMS Basics
A Warehouse Management System (WMS) is sophisticated software that orchestrates the entire symphony of warehouse operations—from inventory management to order fulfillment. Think of it as your warehouse's brain, coordinating everything from the moment goods arrive until they're shipped to your customers. With advanced solutions like OPLOG's smart WMS, businesses can achieve foolproof stock management while maintaining 99.9% order accuracy.
Getting Down to Business: How Does a WMS Work?
Modern WMS solutions do more than just track inventory—they're the command center of your warehouse operations. By integrating seamlessly with e-commerce platforms and ERP systems, a WMS coordinates:
- Real-time inventory tracking and updates
- Efficient order processing and fulfillment
- Optimized storage organization
- Automated picking and packing processes
- Comprehensive shipping management
Consider this order status screen of OPLOG ONE, demonstrating live order tracking from creation to delivery and exemplifying how a WMS can increase the visibility of your operations:
The Perfect Match: Integration with Other Systems
One of the greatest strengths of a modern WMS is its ability to play well with others. Like OPLOG's proprietary system, leading WMS solutions offer seamless integration with:
- E-commerce platforms
- Enterprise Resource Planning (ERP) systems
- Transportation Management Systems (TMS)
- Customer Relationship Management (CRM) tools
- Accounting software
Warehouse Wins: Benefits of Implementing a WMS
Having a system for warehouse management will ease your general workflow. You will notice differences like accurate inventory, adept operations, and enhanced customer service. It's an all-around business boost – from the ground floor workers to client-facing operations.
Precision Perfect: Improved Inventory Accuracy
Say goodbye to the "where-did-I-put-that" syndrome. A WMS provides real-time tracking and automated data entry, reducing errors and keeping your stock counts accurate. OPLOG's WMS, for instance, maintains 100% foolproof stock management through its innovative tracking system.
Speed, Speed: Enhanced Operational Efficiency
Modern WMS solutions include picking robots that eliminate the need to walk around the warehouse, replacing humans at several steps of the fulfillment process. For instance, powered by cutting-edge technology, OPLOG's picking robot TARQAN can:
- Optimize picking routes for maximum efficiency
- Reduce warehouse travel time by up to 400%
- Accelerate order fulfillment
- Streamline receiving and put-away processes
Customer Satisfaction Champions: Better Service
With precise order fulfillment and reliable delivery times, your customers will thank you. Real-time tracking, accurate stock counts, and predictive analytics help maintain high satisfaction levels and encourage repeat business.
Take a look at this OPLOG ONE screen, showcasing automated return analysis:
It is an example to help you better understand how a real-time tracking system, the first-born of a WMS, can help you reach daily information regarding your operations and offer insightful data.
Choose Your Champion: Types of Warehouse Management Systems
Within the scope of warehouse management systems, there are three main categories. These include standalone, ERP-integrated, and cloud-based technologies. Depending on your needs, scale, and budget, a type may be more appealing to certain business models.
Standalone WMS
This type of system exists on the company property and utilizes its own hardware.
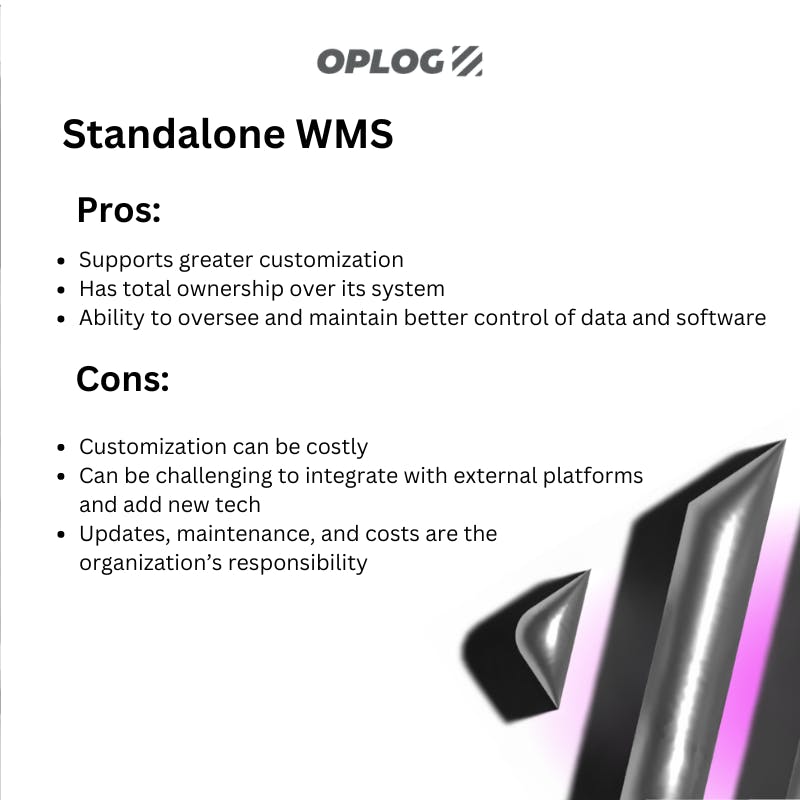
ERP-Integrated WMS
These systems are integrable applications for supply chain and ERP platforms.
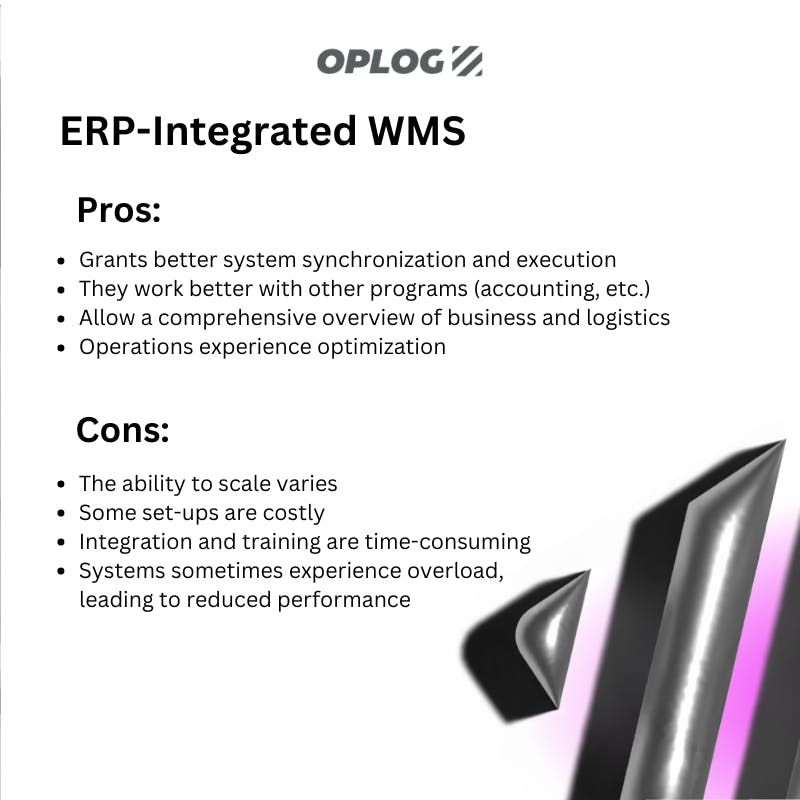
Cloud-Based WMS
Cloud-based refers to a system hosted via the internet. They are delivered as software-as-a-service (SaaS).
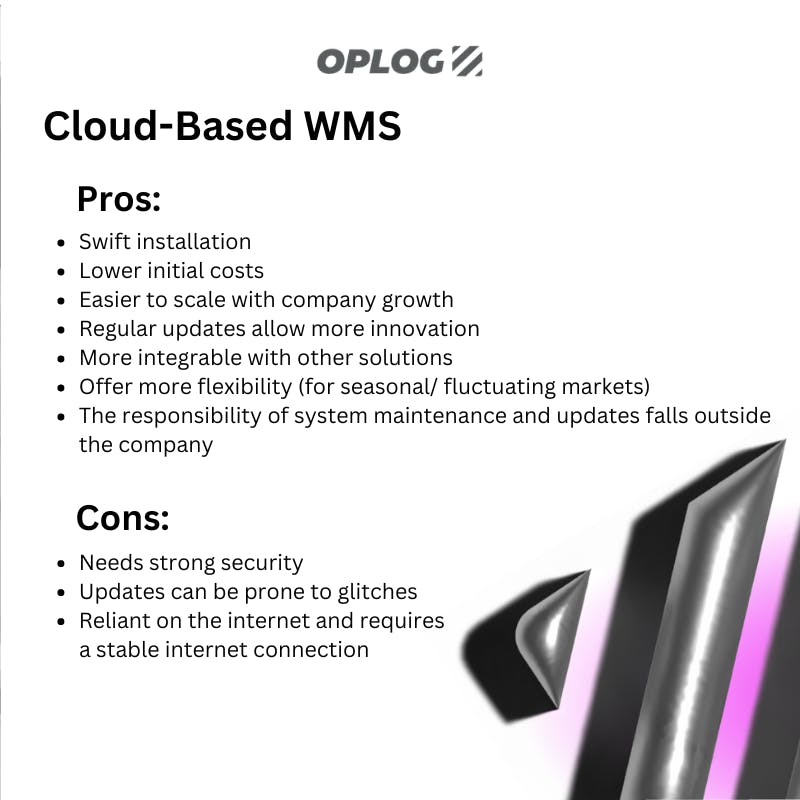
Choose Wisely: Finding Your Perfect WMS Match
Selecting the right WMS isn't just about features—it's about finding a solution that grows with your business. Let's break down the selection process into manageable steps.
Know Your Warehouse Inside Out
Before diving into WMS options, take stock of your current operations:
- Map out your existing workflows
- Identify bottlenecks and pain points
- Document your inventory management processes
- Analyze your current technology stack
OPLOG's experience shows that understanding your current operations is crucial for selecting a system that truly addresses your needs rather than creating new challenges.
Define Your Must-Haves
Create a clear list of requirements based on:
- Current operational needs
- Growth projections
- Industry-specific requirements
- Integration necessities
- Budget constraints
Consider both immediate needs and future scalability—your WMS should grow alongside your business.
Set Clear Goals
Establish specific, measurable objectives for your WMS implementation:
- Target inventory accuracy rates
- Expected processing time improvements
- Desired customer satisfaction levels
- ROI expectations
- Specific efficiency metrics
Integration Capabilities
Ensure your chosen WMS plays well with:
- Your current e-commerce platforms
- ERP systems
- Shipping and carrier services
- Accounting software
- Customer service tools
Look for solutions that offer seamless integration with hundreds of marketplaces and platforms via Open API.
Technical Requirements
Evaluate the technical aspects:
- Hardware compatibility
- Network requirements
- Security protocols
- Backup systems
- Mobile accessibility
Budget Considerations
Factor in all potential costs:
- Initial software investment
- Implementation expenses
- Training requirements
- Ongoing maintenance
- Potential upgrade costs
Consider flexible options like OPLOG's "pay-as-you-go" model, which eliminates fixed costs and hidden fees. This is called "no-contract fulfillment", distinguishing fulfillment providers adopting this payment method from others.
Vendor Evaluation
Investigate available solutions and companies while choosing your WMS. When researching WMS providers:
- Check their industry experience
- Review client testimonials
- Evaluate support services
- Assess their financial stability
- Consider their innovation track record
Conduct A Needs Analysis
This measures the space for improvement between existing operations and targets. Lay out workflow maps to see what data is needed, where, for each step of decisions. Again, gather team input from those who will work in close contact with your system.
Plan For Implementation and Training
After all other assessments are complete, create a WMS roll-out timeline. This will need stages for testing, feedback, and staff training. Teams need to feel happy with their software understanding, while data needs prepping for data migration.
Future-Forward: WMS and Emerging Technologies
The warehouse of tomorrow is already here, with cutting-edge technologies transforming how WMS operates. Let's explore how these innovations are reshaping the fulfillment landscape:
AI and Automation: Your Warehouse's New Best Friends
Artificial Intelligence isn't just a buzzword—it's revolutionizing warehouse management. Through machine learning algorithms, modern WMS solutions like OPLOG's can:
- Predict inventory needs before stockouts occur
- Optimize picking routes in real-time
- Automate decision-making processes
- Enhance accuracy in order fulfillment
Speaking of automation, OPLOG's award-winning robot TARQAN showcases how robotics can transform warehouse operations, achieving 99.99% picking accuracy and 400% faster order fulfillment compared to manual processes.
IoT: Making Your Warehouse Smarter
The Internet of Things (IoT) turns your warehouse into a connected ecosystem where every asset communicates in real-time. Through sensor networks and smart devices, IoT integration enables:
- Real-time location tracking of inventory
- Automated temperature and condition monitoring
- Predictive maintenance for warehouse equipment
- Enhanced security and access control
Implementation: Making Your WMS Work for You
When it comes to finally introducing a WMS into your warehousing set-up, there are a few key points to keep in mind. It is vital to have a sound plan to ensure a smooth transition for effective implementation. When in doubt, voice all your concerns with your chosen WMS team to clarify and address action points.
Step 1: Design Your Success
Start with a system that fits your unique needs. Work closely with your WMS provider to customize:
- User interfaces that make sense for your team
- Workflows that match your operations
- Reporting tools that deliver actionable insights
- Integration points with existing systems
Step 2: Data Migration Magic
Ensure a smooth transition by:
- Cleaning and organizing your existing data
- Validating inventory information
- Setting up proper data hierarchies
- Testing data accuracy before going live
Step 3: Train and Test
Success depends on your team's comfort with the new system:
- Provide comprehensive training sessions
- Run real-world scenario testing
- Document processes and create quick reference guides
- Establish a support system for questions and troubleshooting
Step 4: Go-Live Preparation
Before launching:
- Verify all system settings
- Confirm user access levels
- Double-check integration points
- Prepare contingency plans
Step 5: Launch and Monitor
During and after go-live:
- Monitor system performance closely
- Address issues promptly
- Gather user feedback
- Make necessary adjustments
Step 6: Continuous Improvement
Keep your WMS operating at peak performance:
- Regular system audits
- Performance metric tracking
- User feedback collection
- Periodic training updates
Making the Move: Your Next Steps
Ready to transform your warehouse operations? Consider these action items:
- Assess your current warehouse pain points
- Define your must-have WMS features
- Research potential providers
- Request demos and consultations
- Plan your implementation timeline
Remember, a WMS isn't just software—it's an investment in your business's future. With the right system and partner, like OPLOG, you can achieve:
- Enhanced inventory accuracy
- Improved operational efficiency
- Better customer satisfaction
- Increased scalability
- Reduced operational costs
Whether you're handling a few dozen orders or thousands per day, a modern WMS can help you stay competitive in today's fast-paced e-commerce landscape. The future of warehousing is digital, automated, and intelligent—and it's time to be part of it.
Your WMS Questions Answered